RWDC UAV Design
A package delivery drone designed as a response to the 2020 Real World Design Challenege
Bit of context, this was a design proposal that a sub-team of my high school robotics team submitted to a competition called Real World Design Challenge, one of many competitions we participated in during the Covid-19 pandemic when the FRC season was canceled. This post will provide a summary of the design but the full submission document can be found here.
When COVID-19 initially hit our robotics team FRC867 Absolute Value was devastated. We had previously ranked 5th at LA county regionals, the highest the team had ever ranked, spirits were high, our team collaboration was spot on, we had enthusiastic new talents joining the team, and all of a sudden we were told there was no FRC season for the year. Not being so easily discouraged, our team quickly pivoted to other engineering competitions. One of which included the "Real World Design Challenge (RWDC), an annual competition that provides high school students, grades 9-12, the opportunity to work on real-world engineering challenges in a team environment. Each year, student teams were tasked to address a challenge confronting the nation's leading industries. In 2021, the challenge was tackling autonomous package delivery.
Gantt Chart
The Challenge
With online shopping becoming increasingly prevalent in modern times, accelerated by 2020’s worldwide stay-at-home orders, postal services are struggling to keep up with rising demand. This trend will not be short-lived. If the convenience of virtual shopping is to be made accessible by all members of society, a new delivery method must emerge.
Project Goal
The goal of this project is to design an Unmanned Aircraft System (UAS) which can efficiently deliver packages in a 5km radius from an airfield. The aircraft will take off vertically and travel to the delivery location depending on the speed and altitude set by City UAS Traffic Control (CUTC). The vehicle must be efficient and viable for real-world applications, and the company behind it must be profitable. A successful package delivery company will meet all of these requirements while also making a decent profit.
Delivery by air, specifically by Unmanned Aircraft System (UAS), is a promising prospect for the future economy. Properly executed, this new method is fast, efficient, and more environmentally friendly than any other delivery method present today. UAS methods are not restricted by congested roads—their flight corridors offer unparalleled navigational freedom. Autonomy is the future, and the exemption of a deliveryman improves worker safety and streamlines logistics. Modern systems are also entirely electric—fossil fuels are the bane of our planet’s future, and air delivery is practically emission-free.

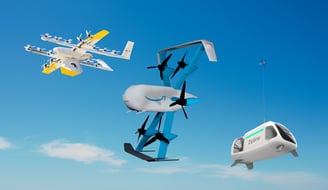
Below is the Gantt Chart our team came up with to plan the engineering side to the project
Research into UAV and VTOL Designs
Below is the Gantt Chart our team came up with to plan the business side to the project
Below are some of the designs we considered
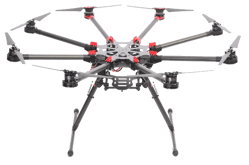

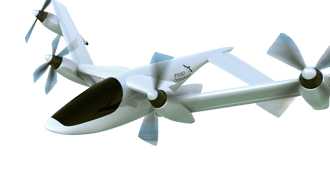
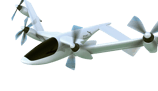
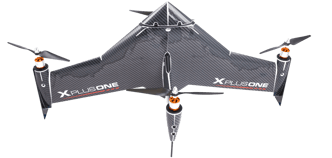
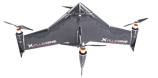
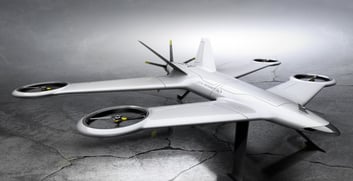
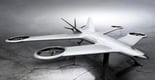
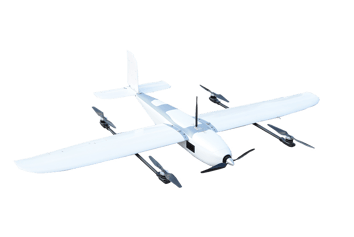
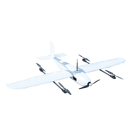
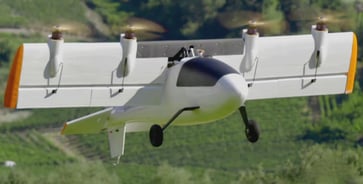
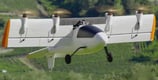
Octocopters
Futura Fixed-Wing VTOL
X PlusOne Tail-Sitter
Pterodynamics Transwing
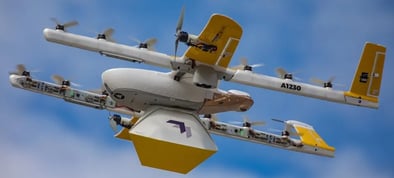
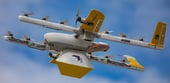
Airbus ThunderBird
Swiss eVTOL Tilt-Wing
Project Wing Prototype
After considering all the designs, we made a decision matrix and a weighted scoring system to decide which design to move forward with
Our Design
We decided to choose a Transwing design, with wings that would rotate at 45 degree angles to transition between a VTOL and a fixed-wing design.
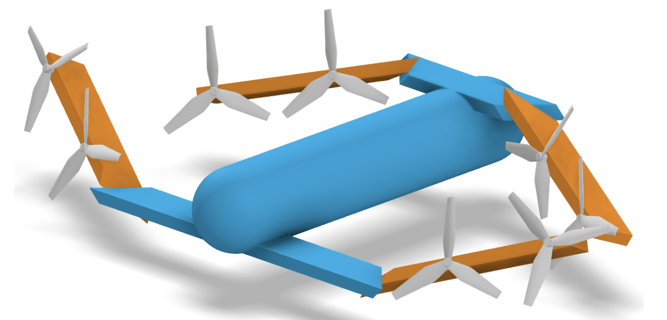
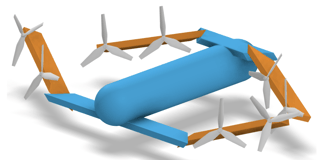
This is the preliminary concept CAD for the Transwing mechanism. Notice how the wings are separated into two parts that meet in a slanted bevel cut, allowing the rotors to fold from a horizontal orientation for the fixed-wing mode to a vertical orientation for takeoff and landing. This is very similar to the Aerodynamics design but with the added redundancy of the extra wings and rotors.
For the materials of the UAV, carbon fiber tubing was chosen for the frame due to its lightweight and rigidity. The UAV spine which runs above the package is built with two carbon tubes in order to increase strength and reduce torsion due to uneven aerodynamic forces on the front and rear set of wings. The wing spars for both the front and rear wings are affixed to the frame itself, eliminating potential weak points that arise with an independent foundation. The exterior of the UAV would consist of a 1mm thick High-Impact Polystyrene (HIPS) shell.
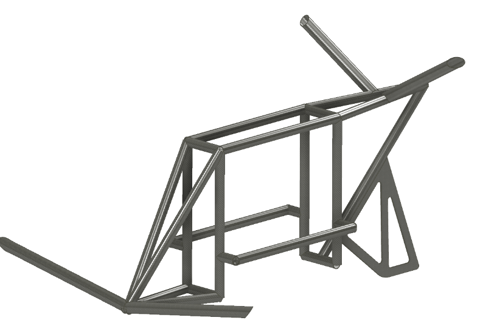
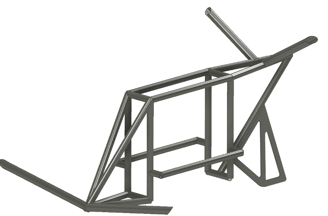
Here is a render of the finalized CAD with the frame exposed for visualization purposes. The sensor suite, including a LiDAR camera would be mounted to the nose of the aircraft for guidance and navigation control
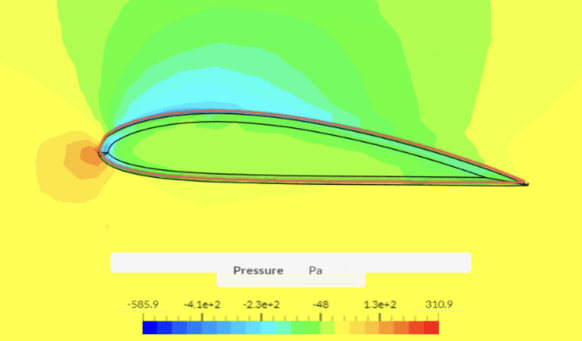
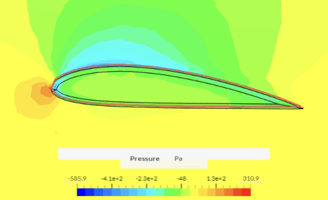
Pressure Diagram of the NACA 4418 airfoil
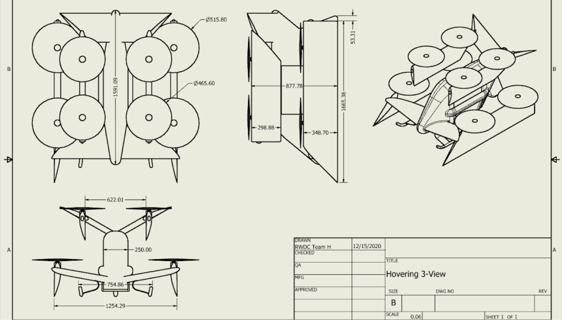
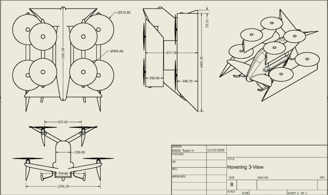
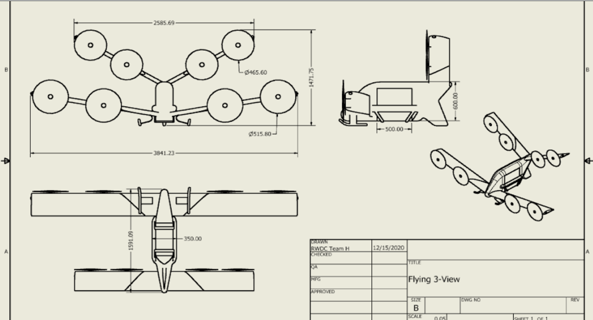
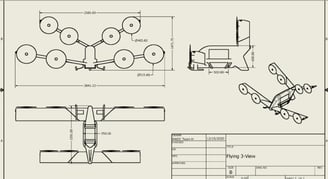
Three View Diagram of the final designs, both in the hovering and flying orientation
Cost Breakdown
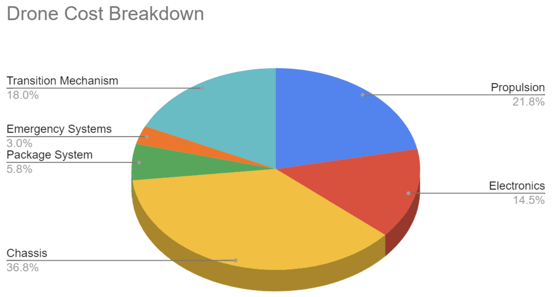
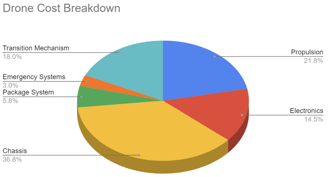
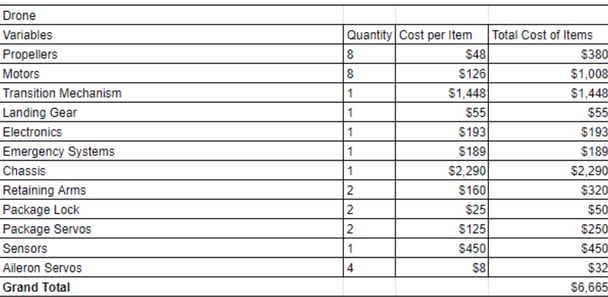
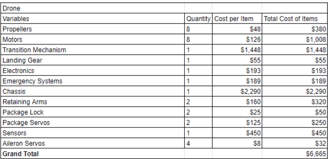
Pie Chart and component table of the estimated cost of the package delivery UAVs.
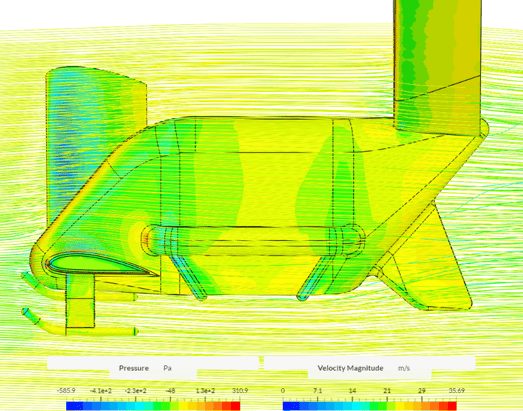
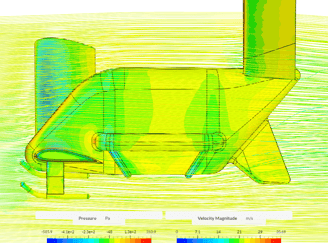
We conducted an aerodynamics simulation and adjusted the angle of attack of the airfoils to get the right lift-to-drag ratio. We did this with both the loaded and empty configuration to ensure the drone would fly properly when heading to the delivery site as well as the returning to the warehouse. The UAV mass was calculated to be about 25kg full, so the minimum lift force required for flight is 245N. I'll spare you details of the lift and drag calculations but if you are curious I have linked the full submission description of this post above.
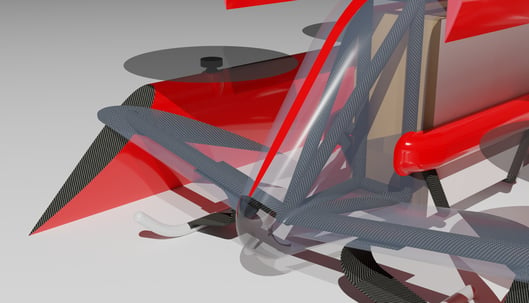
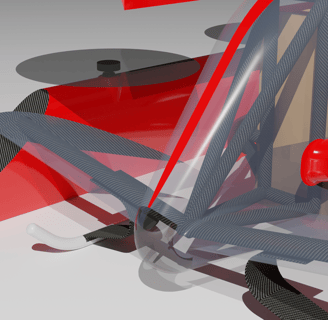
Pressure Diagram of our UAV design
Because the UAV was still a fixed-wing, a proven airfoil had to be chosen, the NACA 4418 airfoil shape was selected after the analysis of the lift and drag polars.
Results
Our submission won second place in the state, but we were able move on to nationals through a wild card draw. In nationals, we were awarded with best first year team.
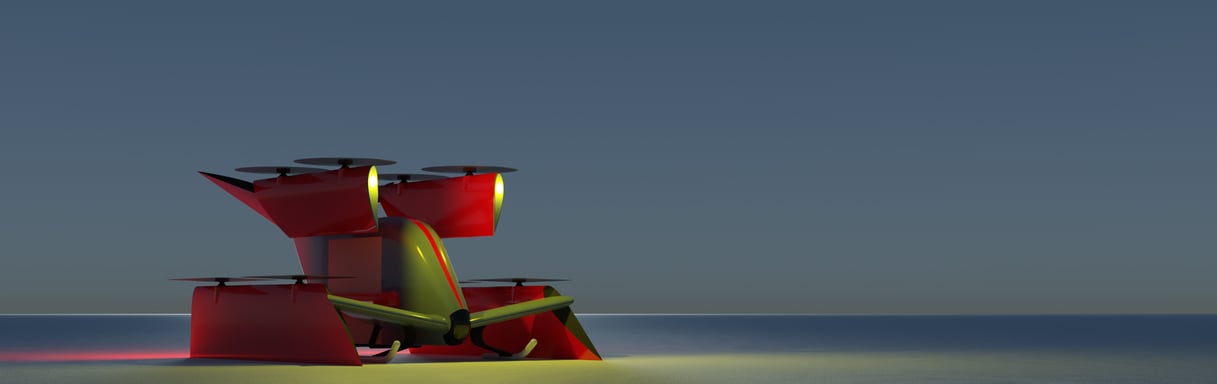
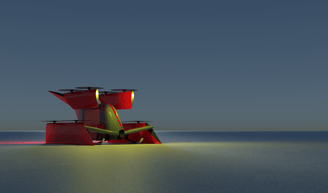